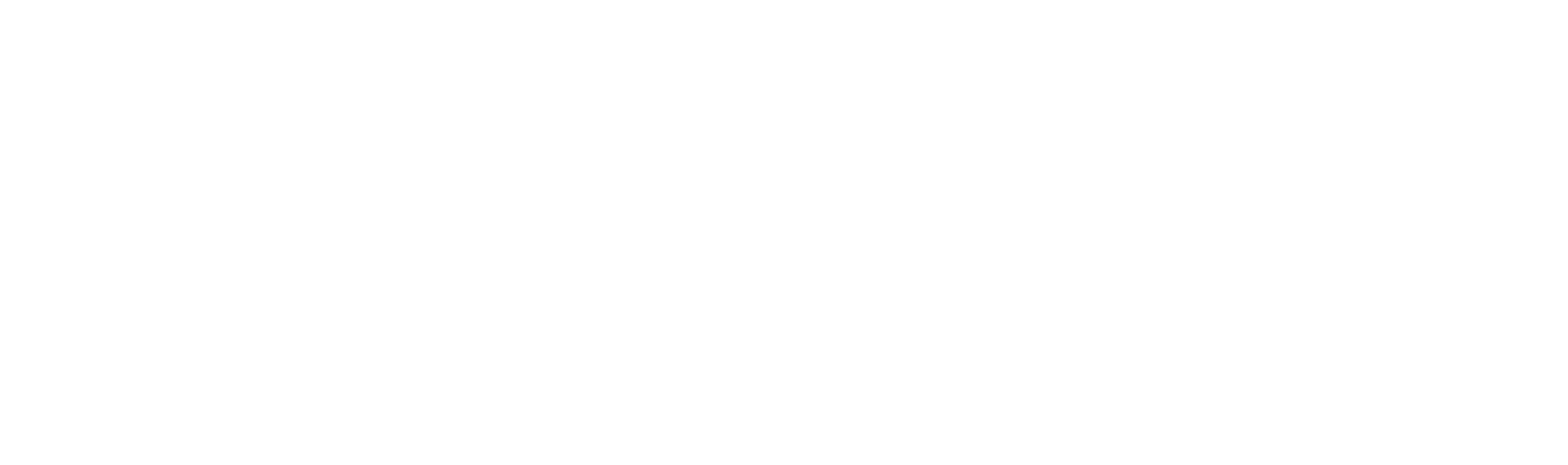
Comprehensive Emissions Monitoring Guide for Refining and Petrochemical Facilities
Your go-to resource for compliance, technology, flaring, and regulatory insights for refinery emissions monitoring.
Understanding Key Regulations
A clear explanation of the rules refineries must follow to manage emissions and stay compliant with environmental laws.
Key Emissions Control Systems
Overview of the primary emissions monitoring systems and technologies.
Flare Gas and Monitoring Solutions
Explores the challenges refineries face in flare monitoring, including variable flow rates, changing gas composition, and harsh conditions.
Data Acquisition and Reporting 101
Details how refineries collect, validate, and report emissions data, addressing the need for data acquisition software and data controllers vs. traditional plant processes.
CEMS Upgrades and QA Testing
How refineries test, maintain, and upgrade continuous emissions monitoring equipment to meet quality standards and regulations.
Real-World Success Stories: Case Studies
Examples of refineries solving compliance challenges, saving money, and staying compliant with effective emissions control solutions.
FAQs
The FAQ section provides straightforward explanations to help clarify technical processes, regulations, and solutions available for improving refinery emissions monitoring.
Understanding Key Regulations for Refining Emissions
Refineries operate under complex regulations aimed at controlling emissions and ensuring environmental compliance. These regulations define pollutants, monitoring requirements, compliance methods, and consequences for non-compliance. Below is an overview of the most relevant rules and their impact on refinery operations.
Understanding the RSR Rule and Compliance Challenges
The Refinery Sector Rule (RSR), finalized by the EPA in December 2015, introduced stricter controls on hazardous air emissions from petroleum refineries. This rule will virtually eliminate smoking flare emissions and upset emission events, and will require refineries to monitor emissions at key emission sources within their facilities and around their fencelines.
However, meeting RSR compliance requirements can be complex, presenting challenges such as:
- Maintaining 15-minute block averages and thoroughly documenting compliance algorithms.
- Implementing enhanced quality control (QC) activities and managing extensive recordkeeping.
- Ensuring operators have immediate access to compliance parameters.
- Storing and making available large volumes of supporting data while reporting deviations.
- Complying with stricter emergency flaring limits without exceptions for startup, shutdown, or malfunctions.
These hurdles can leave many facilities facing compliance gaps. Learn more about Bridging the RSR Compliance Gap – Part 1 and Part 2 to address these issues effectively in monitoring emissions in refineries.
For practical solutions to these specific challenges, our dedicated blog post offers actionable strategies to help you meet the requirements of the RSR.
40 CFR Part 60 - New Source Performance Standards (NSPS)
- Primary Pollutants: Particulate Matter (PM), Sulfur Dioxide (SO₂), Nitrogen Oxides (NOₓ), Carbon Monoxide (CO), and Organic Matter (OM).
- Includes over 90 subparts targeting various pollutants.
- Focuses on facilities using pollution control equipment like scrubbers, baghouses, and catalytic reactors.
- Requires continuous monitoring, daily calibration checks, and annual Relative Accuracy Test Audits (RATA).
- Penalties apply for “excess emissions” or “downtime.”
Read our overview of the EPA 40 CFR Part 60 Regulation for a deeper dive.
NSPS OOOOb & OOOOc
- Addresses methane emissions from refinery equipment and storage tanks.
- Requires advanced leak detection and repair (LDAR) and fenceline monitoring to identify and minimize leaks.
Discover key insights on the EPA’s finalized rules targeting methane emissions in the oil and natural gas sector in our blog, “NSPS OOOOb & OOOOc Rules on Methane: What You Need to Know.”
40 CFR Part 63 - National Emission Standards for Hazardous Air Pollutants (NESHAP)
- Targets 187 hazardous air pollutants (HAPs) like benzene, toluene, and xylene.
- Includes 133 Maximum Achievable Control Technology (MACT) standards for different industry sectors.
- Applies both direct and indirect compliance methods to control emissions.
- Compliance involves regular monitoring, periodic reporting, and adhering to operating permits.
For more information, read our blog post, “What is the EPA 40 CFR Part 63 Regulation?”
Understanding Part 60 and Part 63 Similarities
Both Part 60 and Part 63 require:
- Continuous Emission Monitoring Systems (CEMS) for recording hourly data averages.
- Daily quality checks, including calibration, to ensure data accuracy.
- Annual RATA tests to maintain certification.
- Periodic reports to regulatory agencies. Learn more about Excess Emissions and Performance Summary Reports in our dedicated blog post.
- Monitoring emissions limits, with financial penalties for exceedances.
The regulations also emphasize direct compliance through continuous monitoring and indirect compliance by measuring operating conditions like temperature, pressure, or flow rates.
Emission Control and Operating Permits
Title V Operating Permits consolidate compliance requirements into a single document for ease of tracking. Facilities must ensure emissions stay within permit limits by using equipment like:
- PM Control: Cyclone separators, wet scrubbers.
- NOₓ and CO Control: Catalytic reactors, selective catalytic reduction.
- SO₂ Control: Dry sorbent injection, fluidized beds.
Flares are used to destroy hazardous chemicals during operational upsets, with continuous monitoring to ensure proper combustion.
Monitoring for Escaping Pollutants
Fenceline Monitoring captures benzene levels to measure hydrocarbon leaks, ensuring emissions remain within property boundaries. Devices collect samples over weeks, with wind data determining pollutant dispersion.
This section serves as a foundational overview of refinery regulations and pollutant control methods in monitoring emissions. For a deeper dive, explore these related resources:
Overview of Key Emissions Control Systems and Technologies in Refineries
Refineries employ a range of emissions monitoring technologies to reduce and capture their emissions, including flare monitoring, SRUs, and TGTUs. Pollution control equipment reduces the actual emissions to levels below the permit limits.
Sulfur Recovery Units (SRUs) & Tail Gas Treatment Units (TGTUs)
SRUs and Tail Gas Treatment Units (TGTUs) recover sulfur from refining processes, reducing SO₂ emissions. These systems play a critical role in minimizing refinery impacts and meeting strict environmental laws.
For more details, visit:
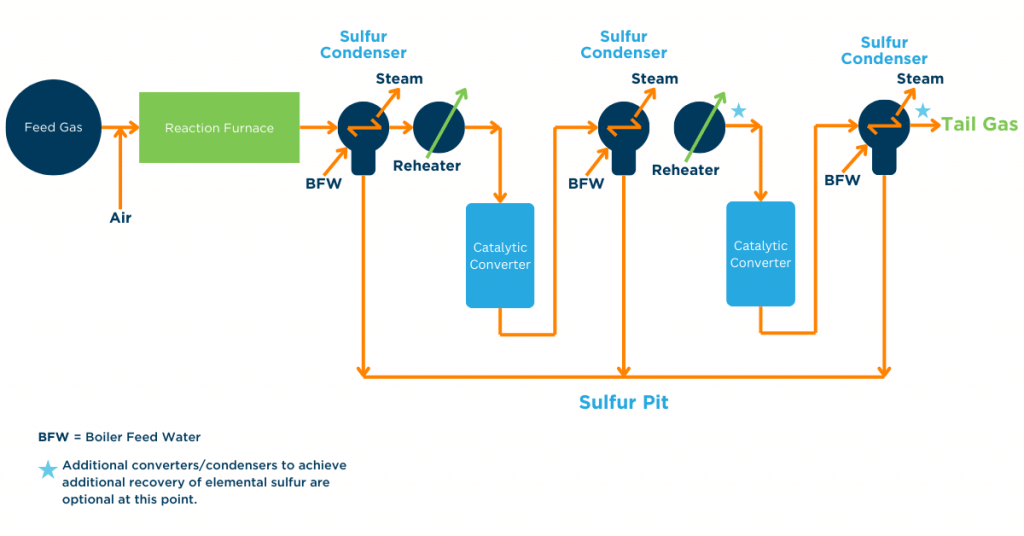
Thermal Oxidizers
Thermal oxidizers destroy VOCs and HAPs by incinerating waste gases at high temperatures. This ensures cleaner emissions and compliance with pollution standards. Learn more about their role: Understanding Thermal Oxidizers and Their Role in Emission Control: Key Insights for the Refining Industry
Additional Emissions Control Equipment
Refineries also use various technologies to control specific pollutants and monitor emissions:
- Wet Gas Scrubbing Systems: Reduce SO₂, NOx, and particulates in fluid catalytic cracking units (FCCUs).
- Selective Catalytic Reduction (SCR): Converts NOx into nitrogen and water using catalysts and ammonia. SCR systems are effective in reducing NOx emissions from combustion processes
- Cyclone Separators and Baghouses: Used for particulate matter control, these systems capture and filter out fine dust and particulates from flue gas streams
- Dry Sorbent Injection and Wet Scrubbers: Common for neutralizing sulfur dioxide (SO₂) emissions, these systems inject chemicals or use liquids to bind and remove pollutants before they are emitted
Fenceline Monitoring
Introduced in 2017, fenceline monitoring ensures that pollutants like benzene do not escape into surrounding communities. Sampling devices continuously record hydrocarbon levels along refinery perimeters.
Flare Gas & Monitoring in Refining Processes
Flares are used in industries like oil and gas and refining to safely burn off extra gases that can’t be reused. This process is important for controlling air pollution and meeting environmental laws. The goal is to turn harmful gases, called volatile organic compounds (VOCs), into carbon dioxide (CO₂) and water. If the burn isn’t complete, it can create harmful byproducts.
To ensure the burn is effective, certain factors need to be monitored:
- Flame temperature.
- How long gases stay in the burning area.
- How well the gases mix during burning.
- Having enough oxygen for the process.
Gas Chromatography Systems
Employed in Continuous Emissions Monitoring Systems (CEMS) to analyze and measure gas composition, particularly in sulfur recovery and flare monitoring.
Challenges in Flare Monitoring
Flare monitoring systems face numerous challenges:
- Changing Flow Rates: The amount of gas can change suddenly, like during emergencies, making measurements harder.
- Different Gas Compositions: The type of gas burned can vary, affecting measurement tools.
- Harsh Environments: Flare stacks deal with high heat and corrosive gases, so equipment needs to handle tough conditions.
- Strict Regulations: Environmental rules require detailed tracking and reporting.
Technologies for Flare Gas Flow Measurement
Advances in measurement technology help overcome these challenges:
- Ultrasonic Flow Meters: Use sound waves for non-intrusive, wide-range flow monitoring.
- Thermal Mass Flow Meters: Rely on heat transfer principles for low-flow accuracy, even with varying compositions.
- Optical Flow Meters: Employ laser or infrared technology, ideal for extreme environments.
Advanced Analytical Techniques
- Mass Spectroscopy: Provides fast (20 seconds per analyte) and highly sensitive measurements for multiple applications using a single analyzer. It reduces costs and increases safety through low-concentration calibrations.
- Gas Chromatography (GC): Separates and identifies organic compounds based on molecular weight and retention time. Compliance with Performance Specification 9 (PS-9) ensures accurate ongoing monitoring of gaseous emissions.
Importance of Staged Flares and Valve Positioning
Staged flares divide the gas load among several stacks to burn it more efficiently. Valves control how much gas goes to each stack, ensuring the system doesn’t overload. This setup helps keep emissions within legal limits and improves safety.
Data Acquisition and Reporting on Emissions for Refineries
Refineries often rely on inefficient methods, such as spreadsheets and plant historian data, for flare monitoring, leading to inaccuracies and operational delays. Regulations such as the Refinery Sector Rule (RSR) and Subpart Ja require precise monitoring of emissions like H2S, Total Sulfur, and BTU content, making reliable systems critical.
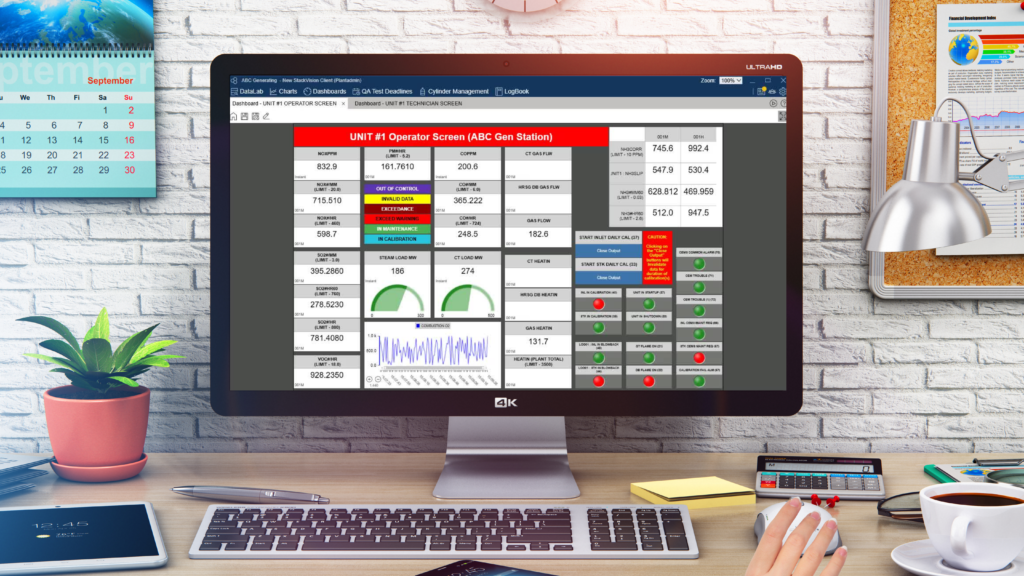
Data Controller vs. Traditional Plant Processes
The 8864 Data Controller, when paired with data acquisition software like StackVision, helps refineries meet the requirements of the Refinery Sector Rule (RSR). Traditional tools like PLCs, DCS, historians and spreadsheets can lead to compliance issues and inefficiencies. The 8864 simplifies data management and reduces the risk of errors when monitoring emissions.
Key benefits include:
- Reducing human error: Automatically filters out invalid data to ensure accurate decisions.
- Saving time on administrative tasks: Automates data capture to prevent errors and reduce manual work.
- Streamlining compliance processes: Consolidates calculations for clearer workflows.
- Improving audit support: Tracks system changes and keeps an accurate record of updates.
- Supporting proactive decision-making: Provides real-time alerts for calibration and operational issues.
Using the 8864 Data Controller helps refineries meet RSR compliance and improve data handling. For more details, read our full blog on using the 8864 in refineries.
How a Data Acquisition System Improves Efficiency in Refineries
Refineries must comply with the EPA’s Refinery Sector Rule (RSR), which includes minimizing flaring and reporting emergency flaring events within tight timeframes.
Key Benefits:
- Real-Time Monitoring: Quickly identify and address emergency flaring events to reduce downtime.
- Predictive Maintenance: Spot potential equipment issues early to avoid unexpected shutdowns and extend equipment life.
- Optimized Operations: Use data to adjust settings for better efficiency and lower energy use.
- Simplified Compliance: A DAS simplifies compliance by automating the collection and reporting of required data, such as 15-minute block averages, quality control parameters, and real-time access to compliance information for operators.
- Improved Safety: Real-time detection of deviations and errors allows for faster responses, helping prevent accidents and improving safety across the refinery.
Learn more by reading our blog, “Improving Operational Efficiency with Data Acquisition Systems in Refineries.”
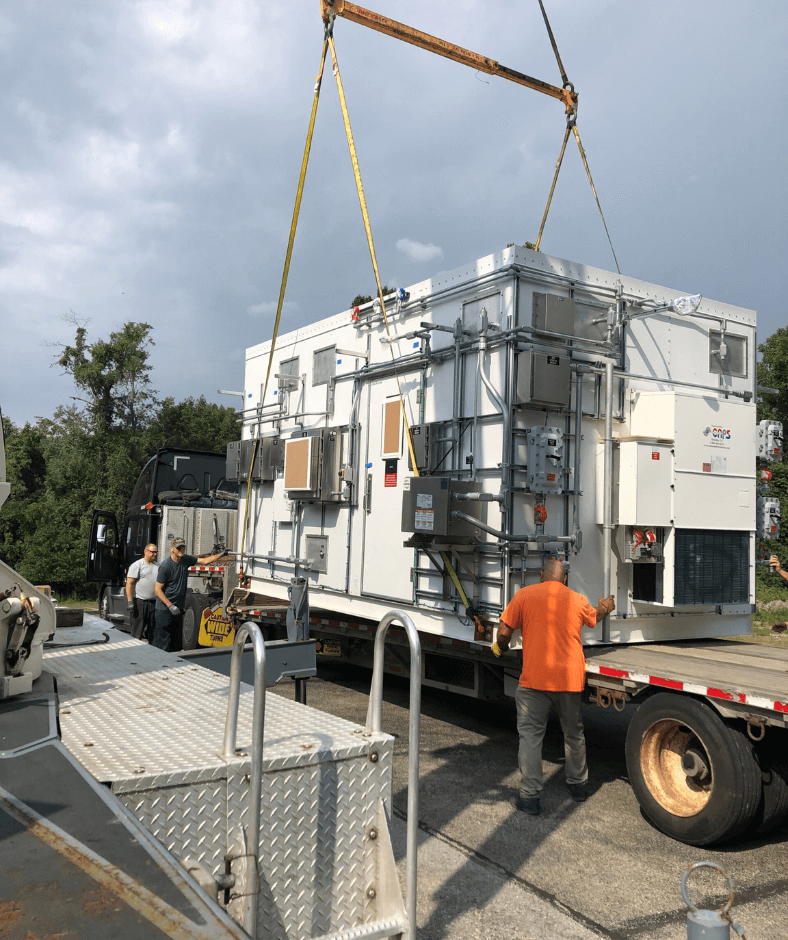
CEMS Upgrades & QA Testing in Petrochemical and Refining
Upgrading CEMS in Refineries
Upgrading Continuous Emissions Monitoring Systems (CEMS) is crucial to maintaining proper emissions monitoring. Refineries can choose from three upgrade options:
1. Component Replacements
For systems in good condition with specific parts needing replacement (e.g., outdated analyzers).
- Pros: Lowest cost, minimal reconfiguration, and reduced labor needs.
- Cons: Risk of future downtime if other parts fail.
2. Full-System Retrofit
For replacing all components while keeping the shelter intact.
- Pros: Saves on shelter costs, keeps critical equipment running, and allows phased upgrades.
- Cons: Higher labor costs, longer downtime, and requires onsite testing.
3. Full-System Replacement
Needed when shelters or major infrastructure are outdated or require relocation.
- Pros: Modernizes the entire system, improves layout, and supports relocation.
- Cons: Highest cost and significant downtime.
Read more about design options and how to plan for a successful upgrade in our blog post, “Upgrading Your CEMS in Refineries and Petrochemical Facilities.”
Data Assessment Reports for CEMS Audits
A DAR consolidates key data from Continuous Emissions Monitoring Systems (CEMS) audits, summarizing quarterly accuracy results and daily calibration drift assessments. It must be submitted alongside emissions reports as specified by regulations, with reporting guidelines detailed in Appendix F to Part 60, Procedure 1, Section 7.
Key Components of a DAR:
- Source Owner/Operator Information: Contact details of the source owner or operator.
- Monitor Details: Specifications and information on the monitoring equipment.
- Quarterly Audit Results: Summary of periodic evaluations.
- EPA Performance Audit Samples: Includes blind sample analysis to assess data bias.
- Corrective Actions: Any steps taken to address discrepancies or issues.
Understanding DARs for CEMS Audits in Part 60
QA Testing in Petrochemical & Refining Facilities
Ensuring safety and compliance in petrochemical facilities requires strict Quality Assurance (QA) practices, especially under regulations like the EPA’s Refinery Sector Rule.
Key Elements of QA Testing
QAQC Manual:
Facilities using Continuous Emissions Monitoring Systems (CEMS) and Continuous Opacity Monitoring Systems (COMS) must maintain an up-to-date QAQC manual. This is required under EPA regulations, including:- 40 CFR Part 75 Appendix B
- 40 CFR Part 60 Appendix F
- 40 CFR Part 63
QA Test Management:
Managing QA tests involves tracking, scheduling, and prioritizing activities. Read how tools like QAInsight simplify these tasks, helping facilities stay compliant and operate efficiently.
Real-World Success Stories: Case Studies
Our case studies section highlights real-world examples of how our solutions have helped refineries address specific challenges in emissions monitoring. By showcasing practical applications, we demonstrate how our technology has improved efficiency in monitoring emissions in the refining industry.
StackVision™ Case Study: Calumet Refinery
StackVision™ Case Study: Petrochemical Plant
FAQs
Why is Total Organic Carbon (TOC) monitoring important in refineries, and how is it done?
Total Organic Carbon (TOC) monitoring is important in refineries to track the level of organic contaminants in water streams, such as wastewater influent and effluent, as well as in condensates. Accurate TOC measurement helps ensure that the water is treated properly before being discharged, meeting environmental regulations. Refineries use specialized TOC analyzers that continuously monitor both high-concentration applications, like wastewater with high solids and salts, and low-concentration systems, such as clean water or condensates. These systems provide reliable results to help refineries maintain compliance with water quality standards.
How do refineries monitor fuel gas BTU and H2S levels?
Refineries must monitor the BTu (British Thermal Unit) and H2S (Hydrogen Sulfide) levels in their fuel gas to ensure safe and efficient operations. This is typically done using reliable and simple sample systems like Gas Chromatographs (GCs), Mass Spectrometers, and Tunable Diode Laser Systems (TDLS). These tools help monitor fuel gas composition while providing accurate data on the energy content (BTU) and hazardous substances (H2S) present in the fuel.
What are the EPA's requirements for fenceline benzene monitoring at refineries, and how does real-time monitoring improve compliance?
The EPA’s Refinery Sector Rule (RSR) requires refineries to monitor benzene concentrations at their fencelines to ensure compliance with air quality standards. Traditional passive sampling methods provide data with a two-week delay, which limits the ability to address issues promptly. Real-time multi-point monitoring systems offer a better solution by providing continuous, up-to-date measurements of benzene levels. This approach allows refineries to quickly detect and respond to potential excursions, reducing the risk of non-compliance.
What monitoring systems are used for Sulfur Recovery Units (SRUs), and how do they improve control and maintenance?
Sulfur Recovery Units (SRUs) and tail gas treating units (TGTUs) rely on several analytical techniques to maintain proper control and ensure compliance. Key monitoring solutions include Feed Forward control, Tail Gas analysis, H2S/SO2 Ratio monitoring, Compliance CEMS, and Sulfur Pit monitoring. These systems provide precise measurements that help refineries optimize performance and meet regulatory standards.
How do refineries ensure compliance with sulfur and nitrogen limits in fuels?
The EPA’s Tier 2 regulations limit the sulfur content in gasoline and diesel to reduce emissions. Refineries use analyzer systems to continuously measure sulfur and nitrogen levels in liquid fuels. These systems rely on methods like X-ray Fluorescence (XRF), which measures sulfur content quickly, and Oxidative Fluorescence, which analyzes sulfur and nitrogen for more detailed results. These measurements help ensure the fuels meet regulatory standards.
Why is Reid Vapor Pressure (RVP) important in refining, and how is it measured?
Reid Vapor Pressure (RVP) is used to measure the volatility of gasoline and other petroleum products. It indicates how easily a liquid turns into vapor at a given temperature, which is important for controlling emissions and ensuring fuel performance. Refineries use specialized analyzer systems to continuously measure RVP in products like gasoline, crude oil, jet fuels, and naphtha. These analyzer systems provide reliable sampling and analysis to ensure that the fuels meet regulatory standards for volatility and performance.
What is physical property monitoring in refineries, and how is it done?
Physical property monitoring in refineries involves tracking key variables such as pressure, temperature, and flow to ensure the proper functioning of refinery processes. These measurements are essential for controlling operations and maintaining safety. Refineries use transmitters to accurately measure these properties.
What is the role of hydrocarbon measurements in refineries, and how can process mass spectrometers (MS) improve these measurements?
Hydrocarbon measurements in refineries are essential for accurately monitoring and controlling various processes. Typically, refineries use Gas Chromatographs (GCs) to measure specific components in the gas or liquid samples. However, process Mass Spectrometers (MS) can replace multiple GCs by offering faster, more reliable, and cost-effective solutions. MS systems can analyze a wide range of hydrocarbons, H2, CO, CO2, and other reactive gases, providing faster analysis times and improving the efficiency of refinery operations. This shift to MS technology helps refineries achieve more accurate results and reduces the need for multiple separate instruments.
Why is distillation analysis important in refineries, and how do simulated and micro distillation techniques improve the process?
Distillation analysis is crucial in refineries for determining the boiling point distribution of distillation column samples, which helps in controlling the distillation process. Accurate boiling point set-points are essential for maintaining column efficiency. Simulated Distillation (SimDist), using GC techniques, is a well-established method, but micro distillation offers a faster and more accurate alternative. By using proven ASTM methods, PAC Micro-distillation provides more precise results and can lead to significant savings in distillation column operation, improving overall refinery efficiency.