What is Flaring?
According to the Environmental Protection Agency (EPA), “Flaring is a combustion control process for organized compound (VOC) in which the VOCs are piped to a remote, usually elevated, location and burned in an open flame in the open air using a specially designed burner tip, auxiliary fuel, and steam or air to promote mixing for nearly complete (>98%) VOC destruction.”
The extent of combustion within a flare is determined by several factors:
- Temperature of the flame
- Duration spent within the combustion zone
- Efficiency of turbulent mixing facilitates the oxidation reaction
- Presence of sufficient oxygen to foster free radical formation
Combustion is achieved when all organic compounds (VOCs) are transformed into Carbon Dioxide (CO2) and water. Incomplete combustion leads to portions of VOCs remaining unchanged or being converted into different organic compounds like aldehydes or acids.
Types of Flares
Flares are generally categorized in two ways: by the height of the flare tip and by the method of enhancing mixing at the flare tip. In all combustion processes, a good air supply and adequate mixing are required to complete combustion. Various flare designs differ due to their accomplishment of mixing.
In most flares, combustion is accomplished by using a diffusion flame. A diffusion flame diffuses air across the boundary of the fuel or combustion product stream toward the center of the fuel flow. This forms an envelope of a combustible gas mixture around a core of fuel gas. On ignition, this mixture establishes a stable flame zone around the gas core above the burner tip.
Steam-Assisted Flares
Steam-assisted flares are single burner tips elevated above ground level that burn vented gas in a diffusion flame. Steam-assisted flares account for the majority of flares installed and are predominantly found in refineries and chemical plants.
Air-Assisted Flares
Air-assisted flares use forced air to provide the combustion air and mixing required for smokeless operation. These flares are built with a spider-shaped burner and many small gas orifices located inside but near the top of a steel cylinder. An air-assisted flare is useful where steam is not available.
Non-Assisted Flare
Non-assisted flares are just flare tips without any auxiliary provision for enhancing the mixing of air into its flame. The use of non-assisted flares is limited to gas streams that have a low heat content and a low carbon/hydrogen ratio that burn without producing smoke.
Flaring Regulations
Federal requirements for flares can be found in the New Source Performance Standards (NSPS) and the National Emission Standards for Hazardous Air Pollutants (NESHAP). The consequences of not properly monitoring and operating within the regulation standards for flares have resulted in lower combustion efficiency and potentially significant quantities of excess emissions of volatile organic chemicals.
The parameters for flares address:
Flares shall be designed for and operated with no visible emissions as determined by the methods specified in paragraph (f), except for periods not to exceed a total of 5 minutes during any 2 consecutive hours.
Flares shall be operated with a flame present at all times, as determined by the methods specified in paragraph (f).
Flares shall be used that have a diameter of 3 inches or greater, are non-assisted, have a hydrogen content of 8.0 percent (by volume) or greater, and are designed for and operated with an exit velocity less than 37.2 m/sec and less than the velocity.
For each flare, the owner/operator shall operate the flare to maintain the net heating value of flare combustion zone gas at or above 270 Btu/SCF determined on a 15-minute block period basis when regulated material is touted to the flare for at least 15 minutes.
Equipment means pumps, valves, pressure relief valves compressors, open-ended lines flanges, connectors, and other equipment covered by the applicable subpart that require monitoring with a 40 CFR Part 60, appendix A-7, Method 21 monitor.
Flare Monitoring
Flare monitoring requirements can be found in §63.987, which states, “Where a flare is used, the following monitoring equipment is required: a device (including but not limited to a thermocouple, ultra-violet beam sensor, or infrared sensor) capable of continuously detecting that at least one pilot flame or the flare flame is present.”
Gas Chromatography is a common method used in flare monitoring to measure and identify organic compounds on the basis of molecular weight, characteristic fragmentation patterns, and retention time.
Read more about Gas Chromatography in our recent blog post outlining out the PS-9 Regulations.
Another common flare monitoring method used is Mass Spectrometry, which involves heating a substance and placing it in a vacuum; the resulting vapor is exposed to a beam of electrons that causes ionization to occur, and following separation is identified based on their mass.
ESC Spectrum brings 30+ years of expertise in process and environmental monitoring and reporting and fully understands Mass Spectrometry technology. Learn more about our experience in Mass Spectrometry for Flare Monitoring.
Flow Monitoring
Flow monitoring requirements can be found in §63.670, which states, “The owner/operator shall install, operate, calibrate, and maintain a monitoring system capable of continuously measuring, calculating, and recording the volumetric flow rate in the flare header or headers that feed the flare as well as any flare supplemental gas used.”
Flare gas is subject to fluctuating velocity ranges and mixed compositions, which can affect measurement accuracy. Ultrasonic Gas Flowmeters are a common method used to measure flare gas by using acoustic vibrations to measure the flow rate.
Industry-Leading Flare Monitoring
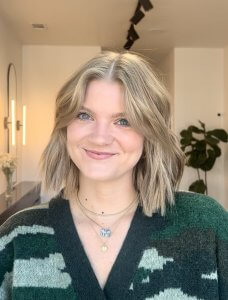
Reagan Sokolosky - Marketing Specialist III
Reagan is a Strategic Communications graduate from Oklahoma State University who joined ESC Spectrum in April of 2020. She dove headfirst into the air emissions compliance industry with no prior experience. She has been writing and researching about air emissions for 4 years to educate our customers. Within four years, Reagan advanced to Marketing Specialist III, showcasing expertise in ESC Spectrum’s learning offerings, email marketing, video editing, product and software releases, and company rebranding.