Company
A leading, integrated, downstream energy company
Industry
Petrochemical
Facility
Plant
Challenges
-
Pass/fail emails were time consuming and difficult to read.
-
DCS alarms in the central control room were difficult to notice and frequently missed.
-
No remote visibility or control of Analyzer shack operations.
Solution
Summary
The refinery installed StackVision on the four refinery flare gas chromatograph (GC’s) that had the most downtime and were not providing operators with much data. The GC’s were connected to an analyzer network for remote access that utilized MODBUS for communication and allowed for remote calibrations and CGA’s.
Benefits
The refinery received data directly from analyzers automatically. The information included detailed reports on daily calibration, weekly calibration trends, and immediate pass/fail notifications via text alerts (eliminating false call-outs from PI issues).
Return on Investment
The proactive calibrations reduced GC Emergency Work Orders (EWO’s) by 50% and allowed the refinery to save over 500 PM man hours per year. CGA hours were reduced by 50% due to StackVision’s automated reporting and immediate pass/fail notifications.
Overall, the 50% reduction in analyzer EWO’s resulted in an overall cost savings of $71,000. The reduction in overall analyzer work orders resulted in cost savings of $207,500. Compared to 2019, the refinery saw a 48% reduction in Continuous Emissions Monitoring downtime and an 83% reduction in unscheduled downtime.
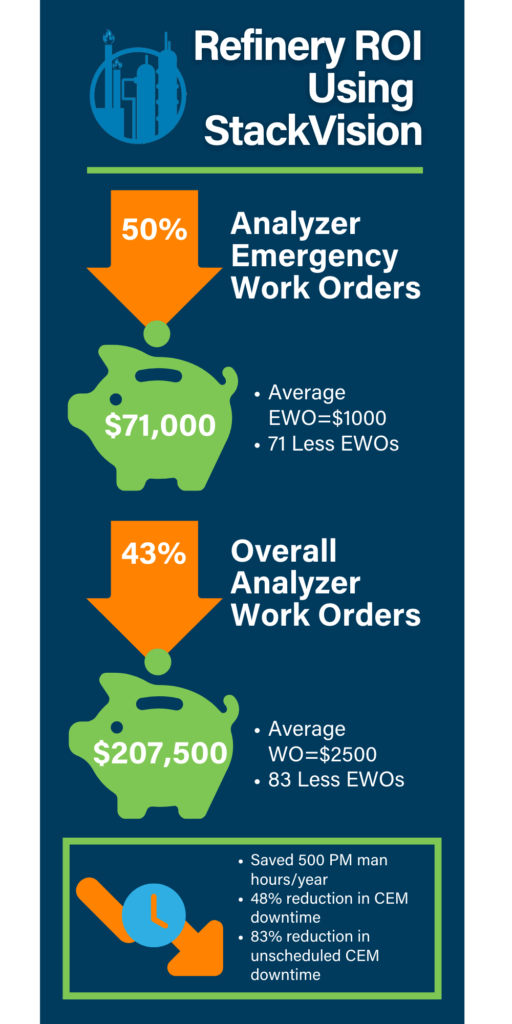