What are Tail Gas Treatment Units (TGTUs)?
Tail Gas Treatment Units (TGTUs) are critical components in the refining and natural gas processing industries, where they play a vital role in sulfur recovery and emissions control. With increasing environmental regulations and the need for more efficient processing, TGTUs have become indispensable for refineries and gas plants aiming to minimize sulfur emissions. This blog post will dive into the technologies and processes behind TGTUs, their role in Sulfur Recovery Units (SRUs), and their importance in meeting stringent environmental regulations.
According to the EPA, Tail Gas Treatment methods include any one or a combination of:
- Catalytic reduction to convert as much of the tail gas sulfur compounds to H2S (coupled with amine adsorption or Stretford solution education);
- Amine adsorption to recover and recycle any H2S present in the tail gas; and
- Incineration to convert the remaining tail gas sulfur compounds to SO2.
The Role of Tail Gas Treatment in Sulfur Recovery Units (SRUs)
Sulfur Recovery Units (SRUs) are designed to extract sulfur from hydrogen sulfide (H2S)-rich gas systems, typically produced during the refining of oil or natural gas. The most common method employed in SRUs is the Claus process, where H2S is converted into elemental sulfur through thermal and catalytic reactions. However, even after Claus treatment, tail gas streams often still contain small amounts of unconverted sulfur compounds like sulfur dioxide (SO2), carbonyl sulfide (COS), and H2S.
Read our blog post, “Enhanced Sulfur Recovery Unit (SRU) Data Collection and Reporting 101,” for a comprehensive look at SRU emissions monitoring.
Tail Gas Treatment Units are designed to capture and further reduce these sulfur compounds in the Claus tail gas stream. By doing so, TGTUs ensure higher overall sulfur recovery efficiency, reducing sulfur emissions to meet stringent regulatory limits. This process is essential not only for maximizing the recovery of valuable sulfur but also for mitigating the environmental impact of refinery operations.
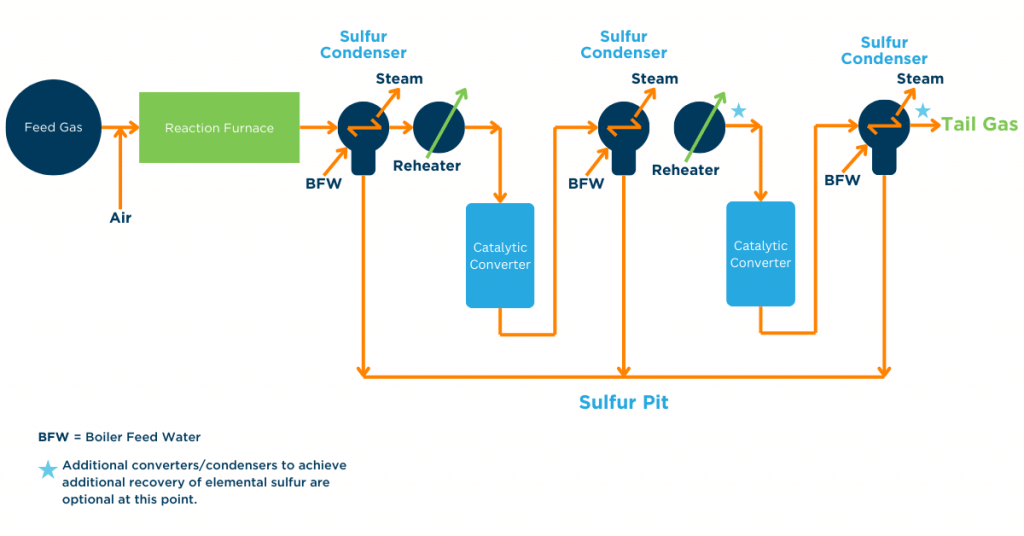
Key TGTU Technologies and Processes
Tail Gas Treatment Units typically employ one or more technologies to reduce sulfur emissions in the tail gas stream. Some of the most common approaches include:
1. Hydrogeneration and Hydrolysis
In this process, tail gas is first treated with hydrogen in the presence of a catalyst, which converts sulfur compounds like SO2, COS, and CS2 into H2S. This hydrogenated gas is then processed in an amine treatment system to absorb H2S, leading to a final gas stream that is largely free of sulfur compounds.
2. Amine Scrubbing
Amine-based absorption is a widely used method for removing H2S from gases. In TGTUs, amine solvents are used to capture H2S into SO2, which is then emitted into the atmosphere. However, this method is less common due to stricter limits on SO2 emissions.
3. Thermal Oxidizers
Sometimes used as an alternative or supplementary process, thermal oxidizers combust the tail gas to convert residual H2S into SO2, which is then emitted into the atmosphere. This method is less common due to stricter limits on SO2 emissions as well.
4. Direct Oxidation
Some TGTUs may employ oxidation technologies that directly convert H2S to sulfur or SO2. This method can be efficient for achieving compliance with emissions standards, but it is not as commonly used as hydrogenation or amine scrubbing in modern refineries.
Regulatory Requirements and Environmental Impact
Regulative authorities like the Environmental Protection Agency (EPA) have focused on the environmental impact of sulfur emissions from refineries. The EPA has highlighted the need for enhanced sulfur recovery technologies to limit emissions of SO2, a precursor to acid rain that poses significant health risks to human populations (EPA 1998 Refinery Initiative).
The Clean Air Act mandates stringent controls on emissions from refinery operations, including those related to sulfur recovery processes. Facilities must comply with federal New Source Performance Standards (NSPS) for controlling SO2 emissions and meet National Ambient Air Quality Standards (NAAQS). Tail Gas Treatment Units are an essential part of ensuring compliance with these regulations.
Modern TGTUs can achieve sulfur recovery efficiencies of up to 99.9%, significantly reducing the refineries’ environmental footprint. This makes them a crucial component in the effort to minimize air pollution and ensure the sustainable operation of refinery facilities.
A Vital Piece of Refinery Infrastructure
In addition to ensuring effective sulfur recovery, Tail Gas Treatment Units (TGTUs) in refineries face several operational challenges. One of the primary pain points is data collection and accessibility, specifically for 1-hour averages, calibrations, and CGAs. This data must be readily available across teams like environmental, field technicians, and corporate-level stakeholders.
Our Data Acquisition System (DAS) StackVision offers flexible tools to support network integration and provide real-time alerts for CMS compliance issues, such as calibration failures, maintenance needs, analyzer malfunctions, and permit limit exceedances. StackVision seamlessly integrates with TGTUs to streamline data collection via analog, Modbus, or data historians.
"The TGTUs are subject to Part 60 Subpart J/Ja and Part 63 Subpart UUU, which largely points back to J/Ja. The system is installed to comply with the limits specified in J/Ja or UUU and any permit requirements. The DAS provides reports around those limits, downtime, calibration/CGA records and other reports that may be useful for the site such as calibration trends and bottle pressures to ease technician responsibilities."
Thermal oxidizers and TGTUs must also meet specific regulatory standards, and StackVision supports compliance by generating essential reports for SO2 and O2 analysis, calibration trends, and bottle pressures to optimize technician workflows. These features make StackVision the preferred choice for sites aiming to meet complex regulatory requirements and achieve optimal TGTU performance.
For a complete resource on emissions monitoring, explore our Comprehensive Emissions Monitoring Guide for Refining and Petrochemical Facilities, covering everything from best practices to regulatory compliance.
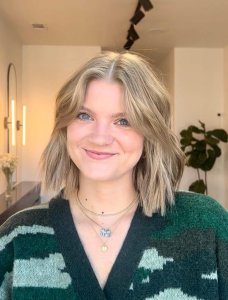
Reagan Sokolosky - Marketing Specialist III
Reagan is a Strategic Communications graduate from Oklahoma State University who joined ESC Spectrum in April of 2020. She dove headfirst into the air emissions compliance industry with no prior experience. She has been writing and researching about air emissions for 4 years to educate our customers. Within four years, Reagan advanced to Marketing Specialist III, showcasing expertise in ESC Spectrum’s learning offerings, email marketing, video editing, product and software releases, and company rebranding.
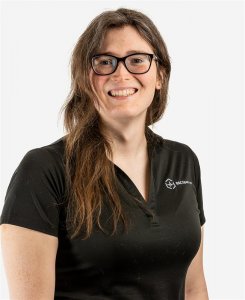
Alexis Ferguson - Lead Senior System Implementation Engineer I
Alexis Ferguson is the technical lead over refining and petrochemical facilities for ESC Spectrum. She holds a bachelor’s in chemical engineering and started working with ESC Spectrum in DAHS implementation for power gen clients nine years ago. Alexis has spent the past six years focusing on designing, implementing, and developing standards for refinery and petrochemical DAHSs encompassing the refinery sector rule (RSR), J/Ja, GHG, and most recently, Ethylene, MON, HON, and OLD MACTs. She has worked with dozens of refining and petrochemical facilities and acts as a technical resource for her coworkers. Outside of work, she is an avid board game hobbyist and brings a “game on” attitude to meeting the DAHS needs of her clients.