In 2007, the Environmental Protection Agency (EPA) modified the definition of chemical process plants and how ethanol plants are categorized, affecting ethanol regulations for CEM systems. Ethanol is either produced for fuel, industrial use, or human consumption.
Before the 2007 EPA’s rule changes, corn milling facilities that produced only ethanol for fuel use were considered chemical process plants, unlike facilities that produced ethanol for human consumption.
The result of this rule change is ethanol plants, regardless of what the ethanol is produced for, must demonstrate compliance with various air quality emission standards as it applies to three Clean Air Act permitting programs, including the PSD permitting program, nonattainment NSR, and Operating Permits (Title V).
EPA’s Air Permits in the Ethanol Industry for Part 60 Regulations
These air permitting programs rely upon emissions thresholds to determine when program requirements will apply to a facility/plant. If your ethanol facility has the potential to emit target air pollutants in amounts equal to or greater than the threshold, you’ll be required to obtain permits that outline emission controls in 40 CFR Part 60. Gain a clearer understanding using our Part 60 Monitoring Plan Overview.
This final rule establishes that the thresholds for facilities producing ethanol, using corn or other carbohydrate feedstocks, have increased from 100 tons per year to 250 tons per year for the PSD permitting program.
The threshold for the nonattainment NSR and Title V programs will remain at current levels. Additionally, fugitive emissions from ethanol plants do not need to be included when determining the emission threshold for PSD or Title V.
Under the final rule, permitted emissions limits and other requirements for existing sources remain in effect. These limits and other requirements may only be modified through a permit revision demonstrating that modifications meet all requirements that apply to the facility and will not contribute to air quality that would violate the National Ambient Air Quality Standards. Read more about the final rule here.
How long does CEMS equipment last?
After the 2007 ruling, your plant may have added a CEM system to comply with the EPA’s regulations. Analyzers, umbilical systems, and other CEMS equipment typically last about 12-15 years. Many plants are currently repairing and upgrading CEM system equipment this year to maintain regulatory compliance.
CEMS parts like regulators, probes, pumps, coolers, specialty gaskets, sample conditioners, and filters also need to be maintained. It is critical to keep up with your umbilical systems, from its wiring and tubing bundle to the insulation and heated hose, as there are many factors that can cause umbilical systems failures and should be inspected and replaced after 12 – 15 years.
It is important to keep up with all CEM system equipment lifecycles to maintain air emissions monitoring requirements for ethanol facilities. Read more about managing analyzer lifecycles.
Customized CEM Solutions for Your Ethanol Plants
ESC Spectrum provides customized CEMS solutions to ethanol plants for air emissions monitoring and compliance. Upkeep and maintenance of your CEM system equipment for ethanol plants are vital to avoid fines and ensure compliance with Part 60 air emission regulations. ESC Spectrum has over 50 CEMS technicians across the country to serve your ethanol facility’s emission monitoring maintenance needs.
Data Acquisition System for Ethanol Plants
ESC Spectrum offers data acquisition systems for Part 60 applications for EPA reporting compliance. Our data acquisition systems are backed by 24/7/365, best-in-class customer support from a dedicated team of experts, online and in-person training, and are in continuous development to keep pace with ethanol industry changes. We know how crucial customer support and training are to making the DAS work properly for your facility.
Interested in learning more about regulations and staying in compliance with the EPA? Check out our Definitive Guide to Air Emissions Regulations.
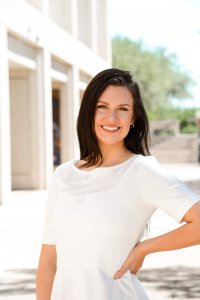
Taylor Hempel - Marketing Specialist II
Taylor Hempel is a skilled marketer specializing in content creation, social media management, and driving customer engagement. With a BBA in Marketing from the University of Texas at San Antonio, she joined ESC Spectrum in February 2022. Taylor is adept at crafting informative content about continuous emissions monitoring systems, its components and data acquisition systems allowing her to craft content that educates and informs industry professionals.