Upgrading CEMS in Refining and Petrochemical Plants
Refining and petrochemical facilities must comply with evolving air emissions regulations, requiring up-to-date emissions monitoring technology. One of the key systems used in these facilities is the Continuous Emission Monitoring System (CEMS).
As technology evolves and regulatory demands increase, upgrading your CEMS and implementing a Data Acquisition (DAS) becomes essential to ensure accurate emissions monitoring and compliance with regulations such as the Environmental Protection Agency’s (EPA) 40 CFR Part 63 (MACT CC) requirements and the Refinery Sector Rule (RSR).
This blog post explores the various options for upgrading your CEMS in refining and petrochemical facilities, detailing their benefits and considerations.
Part 1: Upgrade Options
Option 1: Component Replacements
If most parts in your CEM System are running in good condition, replacing select components of the CEM system is an ideal option. An example would include replacing analyzers that are at the end of their life cycle or facing obsolescence.
Replacing parts over time makes this a cost-effective solution for refineries that need to maintain continuous operations while upgrading their systems.
Pros:
- Least Cost: Focuses on replacing only necessary components, minimizing expenses. This is crucial for refineries operating on tight budgets or needing to allocate funds to other critical areas.
- Minimal Data Acquisition System Configuration Changes: There is limited reconfiguration required, maintaining system continuity. Therefore, refineries can avoid disruptions in their emission data collection and reporting processes.
- Lowest Labor Commitment: Fewer components to replace means reduced labor requirements, which is beneficial for facilities with limited maintenance staff.
Cons:
- Risk of Overlooking Other End-of-Life Equipment: There is a risk for future downtime if other components fail soon after. Refineries must carefully assess all equipment to avoid unexpected failures that could impact compliance.
Option 2: Full-System Retrofit
A full-system retrofit is necessary when all system components such as analyzers, probes, sample lines, and filters need replacement, but replacing the shelter is impractical due to existing operational equipment or space constraints.
This option allows refineries to modernize their systems without the logistical challenges of moving or replacing large shelters.
Pros:
- Cost Savings on Shelter and Major Electrical: Avoids the high costs associated with new shelters, which benefits refineries looking to optimize their capital expenditures.
- Unrelated Equipment Stays Operational: Allows essential equipment to remain functional during the upgrade, ensuring that critical refinery processes are not disrupted.
- Scalable Project: Can be customized to the facility’s specific needs, allowing refineries to prioritize certain upgrades based on immediate regulatory and operational demands.
Cons:
- Highest Labor Costs: Intensive labor is required for multiple component replacements, which can strain refinery maintenance resources.
- Longer Downtime: Extensive work leads to longer operational outages, potentially affecting refinery output and revenue.
- Potentially Messy Execution: May not be as neat and organized as a full replacement, which can be a concern for facilities with strict safety and cleanliness standards.
- Onsite Testing Required: Equipment needs thorough onsite testing, which can be time-consuming and require additional resources.
Option 3: Full-System Replacement
A full-system replacement is the best option when the shelter, cabinet, or rack is end-of-life, the current shelter no longer meets operational needs, or the CEMS requires relocation. This approach provides a fresh start with the latest technology and infrastructure, ensuring refineries meet the highest emissions monitoring standards and regulatory compliance.
Pros:
- Complete Overhaul: Upgrades all outdated components, leading to a modern, efficient setup that enhances a refinery’s ability to monitor emissions accurately.
- Potential for Improved Layout: New shelters can be designed to meet current and future needs, optimizing space and functionality within the refinery.
- Opportunity for Relocation: Optimizes the CEMS location for better operational efficiency, allowing refineries to place the system in a more strategic location.
Cons:
- Highest Cost: Involves purchasing new shelters and all new components, requiring significant capital investment.
- Significant Downtime: Requires substantial downtime for complete system replacement, which can impact refinery operations and production schedules.
Part 2: Design Options
When upgrading CEMS, refining and petrochemical facilities have several design options to consider. These options allow refineries to customize their CEMS shelters and enclosures to meet specific operational and regulatory needs, enhancing efficiency and compliance.
The following are some examples of the custom designs that we offer:
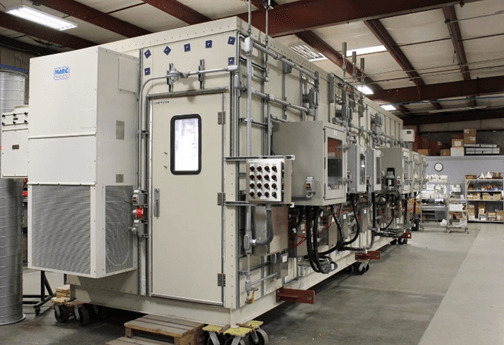
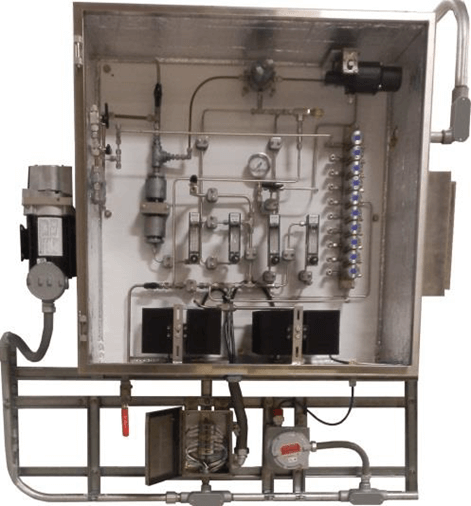
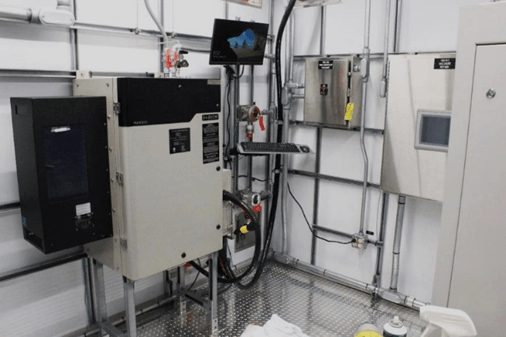
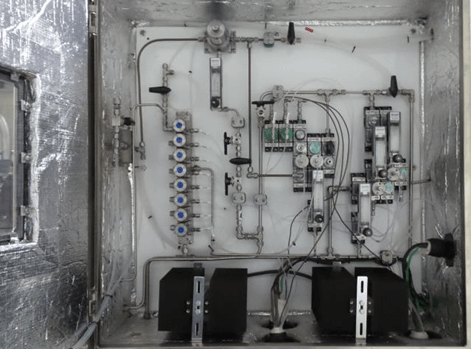
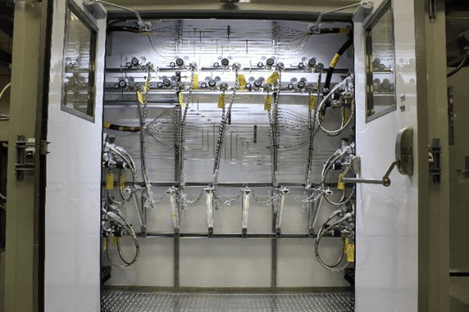
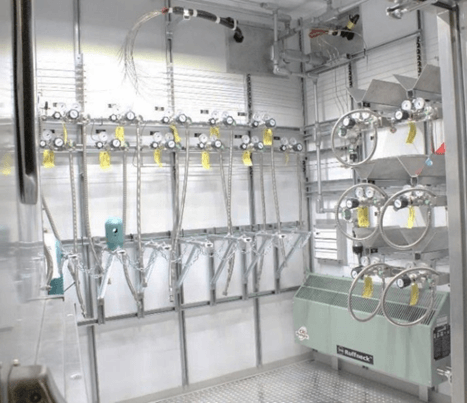
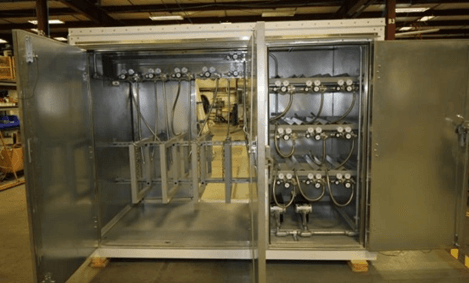

Part 3: Planning
Proper planning is crucial for a successful CEMS upgrade in refineries and it is important to coordinate closely with vendors and internal teams to ensure that there is time for the following steps to be completed:
Timelines
- Requisitions and approvals
- Purchase Order (PO) process
- Design approvals
- Long lead-time items
- Shipping
- Labor availability
- Installation
- Certification
Deciding Scope and Responsibilities
Additionally, refineries that are planning CEMS upgrades will need to clarify the scope of work and assign responsibilities for:
- Removal of existing equipment
- Placement of new equipment
- Installing sample lines
- Equipment start-up
- Certification
- Fenceline Monitoring Plans for Benzene and other required pollutants and Community Air Monitors, if applicable to your facility based on federal, state, and local mandates
- Continuous Monitoring System (CMS) Plan Updates
- Drawings
- Operation & Maintenance (O&M) Manuals
We offer multiple resources to help keep your facility in compliance. Read our blog post, “Decoding the World of Flare Gas Monitoring” to learn more about flare monitoring regulations and how your facility can stay in compliance.
For a complete resource on emissions monitoring, explore our Comprehensive Emissions Monitoring Guide for Refining and Petrochemical Facilities, covering everything from best practices to regulatory compliance.
How ESC Spectrum Can Help
Upgrading CEMS in refining and petrochemical facilities is a vital step in maintaining compliance with regulations such as the Environmental Protection Agency’s 40 CFR Part 63 (MACT CC) requirements and the Refinery Sector Rule (RSR).
ESC Spectrum has staff with decades of professional experience providing custom CEMS solutions across a wide array of industries, whether for new installations, partial upgrades, spare parts, or maintenance assistance.
We have decades of experience creating integrated CEMS systems for the natural gas, liquid natural gas, and liquid hydrocarbon sectors, process and flare gas monitoring systems midstream, and systems for fenceline and ambient air applications.
Visit our Refining Page and Petrochemical Page to learn more about the various solutions that we offer.
If you think your facility would benefit from implementing our CEMS solutions, contact us today for more information.
Data Acquisition in Refineries: Plant Process Systems vs Data Controllers
Case Study: Seamless Integration at Lightstone Energy, LLC
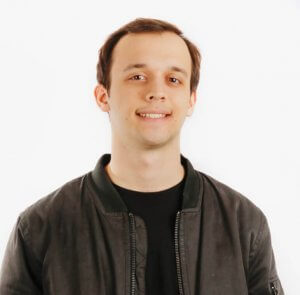
Dan Napolitan - Marketing Specialist I
Daniel joined ESC Spectrum in August of 2023 as a Marketing Specialist I. He started this position shortly after graduating from the University of Missouri with a degree in Journalism and Strategic Communications. Prior to working with ESC Spectrum, Daniel gained experience in the digital marketing field doing SEO and keyword research to produce successful organic content. He is now responsible for completing various marketing tasks such as blog writing, social media posts, paid search advertisements, web analytics, and more.