Refineries face increasing challenges regarding emissions management and EPA compliance, particularly with tracking requirements for flares and valve positioning. This blog delves into the importance of staged flares and valve positioning for emissions monitoring systems. Additionally, we will discuss how leveraging data-driven operations can help refineries improve their efficiency in managing flare systems.
Overview of Staged Flares
Staged flares are a type of flaring system used in refineries and petrochemical plants to manage excess gases produced during processes. Unlike traditional flare systems, which direct all gases to a single flare, staged flare systems activate multiple flare stacks in a sequence based on gas volume, optimizing combustion efficiency. This setup is crucial for managing emissions and complying with environmental regulations such as the EPA’s NESHAP regulations and Refinery Sector Rule (Science Direct).
The Role of Valve Positioning
Valve positioning plays a crucial role, particularly in systems with staged flares, by controlling the flow of gases that are routed to the flare system for combustion. Proper valve positioning ensures that gas flow is regulated to match the capacity of the flare system. In industrial processes, excess gases (such as hydrocarbons) are often produced and must be safely combusted to prevent the release of harmful emissions. Rather than sending all the gases to a single flare, staged flares divide this load among multiple flare stages or burners.
Operational Dynamics of Staged Flares
The system monitors gas flow and pressure, with valve positioning controlling which stage of the flare is activated. When the gas volume is low, only one stage of the flare is activated. As gas volumes increase, additional stages are brought online to handle the increased load, ensuring the most efficient use of the flare system.
Additionally, valves help in controlling the pressure of the gas entering the flare system. Pressure control is key to ensuring that gases are burned at the correct temperature and with the right air-to-fuel ratio.
By operating in stages, the system can maintain higher combustion efficiency across varying gas volumes, reducing unburned pollutants and minimizing harmful emissions such as volatile organic compounds (VOCs) or hazardous air pollutants (HAPs).
Enhanced Control with Staged Flares
Because the gas volumes can vary significantly during different operational phases of a refinery (such as startups, shutdowns, or maintenance), staged flares provide better control over the flaring process. They prevent overloading a single flare, which can lead to inefficiencies or safety risks.
Incorrect valve positions can result in dangerous over-pressurization or the release of uncombusted gases into the atmosphere, both of which pose serious safety risks.
Automated valve positioning systems, often integrated with real-time monitoring technologies, ensure that the valves respond immediately to changes in pressure or gas volume, thereby maintaining a safe operating environment (OSHA).
The Benefits of Proper Valve Positioning
Proper valve positioning can also help reduce fuel consumption. If gas flow to the flare is not managed correctly, too much gas may be flared, leading to wasted energy. By ensuring that only the required amount of gas is combusted at any given time, valve positioning helps refineries optimize their energy use, thus lowering operational costs.
Automated control systems that track and adjust valve positions in real-time are becoming standard in modern refineries to handle fluctuating gas volumes and to optimize energy use.
Does your facility use general flaring technologies? Read our blog post that explores the details of flaring, including types of flares, operations, applications, and monitoring methods.
Case Study: Calumet Montana Refinery
The implementation of ESC Spectrum’s StackVision software at Calumet Montana Refinery showcases how advanced data acquisition systems can enhance flare operations and regulatory compliance. The refinery, which has a capacity of about 30,000 bbl/day and dates back to the 1920s, has a history of about 30,000 bbl/day.
Following a significant expansion in 2015, Calumet faced challenges with compliance monitoring, particularly under the Refinery Sector Rule (RSR), which mandates rigorous flare minimization and emissions monitoring.
Key Challenges Faced by Calumet:
- Data Collection and Management: The refinery struggled to manage the complex data requirements imposed by RSR, which quadrupled the amount of data that needed to be collected and reported. The existing systems lacked transparency, leading to communication issues between personnel.
- Lack of Configurability: Their previous emissions data system was difficult to modify due to its firewall limitations and required on-site personnel for changes, hindering operational efficiency.
Why Calumet Chose StackVision:
After evaluating multiple solutions, including manual spreadsheets and outdated systems, Calumet selected StackVision for its user-driven, innovative design. The software met the rigorous monitoring and reporting requirements set forth by the EPA and provided a high level of configurability that allowed environmental professionals to manage data directly.
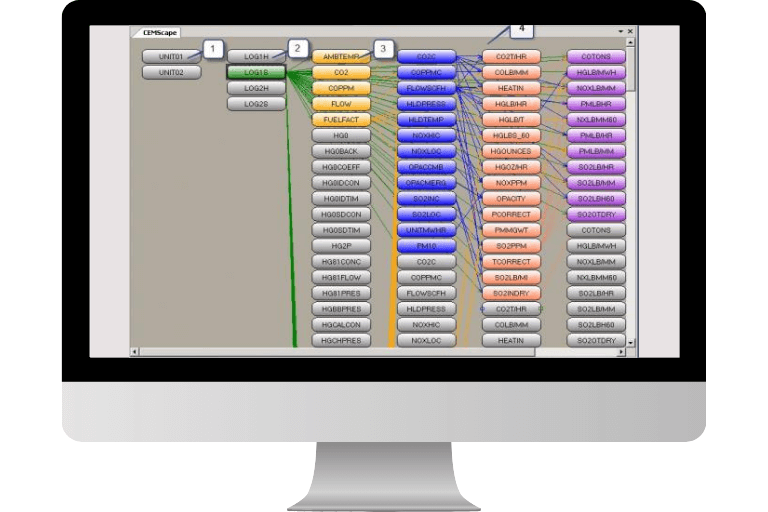
Benefits of StackVision:
- Data Transparency: StackVision allowed refinery personnel to access real-time compliance calculations, enhancing communication and operational transparency.
- Configurability and Ease of Use: The software allowed for remote access and customization, enabling quick problem-solving and efficient reporting.
Joe Dauner, Environmental Manager at Calumet, emphasized that StackVision’s automation facilitated their choice of our DAS software, regarding data handling. This streamlined compliance processes and minimized the recurrence of data quality issues. Read our detailed case study for more information.
For a complete resource on emissions monitoring, explore our Comprehensive Emissions Monitoring Guide for Refining and Petrochemical Facilities, covering everything from best practices to regulatory compliance.
How ESC Spectrum Can Help With Staged Flares & Valve Positioning
In conclusion, staged flares and proper valve positioning are essential for effective emissions management in refineries. The experience at Calumet Montana Refinery illustrates how leveraging advanced technologies like StackVision can significantly enhance flare operations, improve compliance with environmental regulations, and optimize overall refinery performance. Our Reporting and Regulatory team specializes in helping refineries streamline compliance with complex environmental regulations. By providing expert guidance and tailored reporting solutions, we ensure that refineries meet critical requirements like the Refinery Sector Rule and increase data transparency.
By adopting these solutions, refineries can better manage their emissions and maintain a safe and efficient operational environment.
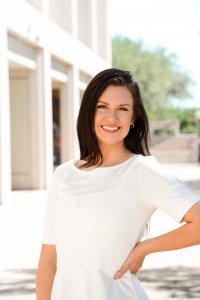
Taylor Hempel - Marketing Specialist II
Taylor Hempel is a skilled marketer specializing in content creation, social media management, and driving customer engagement. With a BBA in Marketing from the University of Texas at San Antonio, she joined ESC Spectrum in February 2022. Taylor is adept at crafting informative content about continuous emissions monitoring systems, its components and data acquisition systems allowing her to craft content that educates and informs industry professionals.
Contact Taylor at thempel@escspectrum.com for questions or comments.