In the complex landscape of refinery operations, adherence to regulatory standards, particularly in air emissions, is critical. Keeping in mind the Environmental Protection Agency’s (EPA) 40 CFR Part 63 (MACT CC) requirements via the Refinery Sector Rule (RSR), refineries seek advanced solutions to ensure compliance. Among these is the 8864 Data Controller, which works with Data Acquisition Software like StackVision to provide a comprehensive approach that aligns with the demands of RSR regulations.
Using the 8864 Data Controller in Refineries and the Risks it Can Prevent
In this regulatory environment, refineries relying on traditional tools like Programmable Logic Controllers (PLCs), Distributed Control Systems (DCS), Historians, or spreadsheets can pose significant challenges, potentially jeopardizing compliance efforts and operational efficiency.
This blog post will highlight some of these challenges, the risks they pose, how they manifest, and how using the 8864 Data Controller in refineries can mitigate risks and streamline the compliance process.
Human Error in Refineries:
Risk: Potential wrong decision-making based on invalid data.
Solution: The 8864 Data Controller paired with Data Acquisition System (DAS) software such as StackVision, automatically excludes invalid data in real-time as it’s recorded from analyzers and measurement devices, ensuring the integrity of the data used for decision-making.
Maintaining Administrative Work:
Risk: Lost time and regulatory reporting errors.
Solution: Without automation, considerable time is spent querying analyzer techs and logbooks for downtime events. The 8864 automates data capture from GC or calorimeter status codes, reducing the risk of reporting errors due to missing or invalid statuses.
Confusion about Underlying Calculations and Workflows:
Risk: Calculations spread across multiple systems lead to mapping and rounding errors, posing challenges for compliance.
Solution: The 8864 Data Controller consolidates all compliance calculations and data processing within its system, providing clarity and transparency in workflows.
Information Lost with Turnover in Refineries:
Risk: Lack of visibility into calculations and changes made by different operational groups.
Solution: The 8864 offers complete transparency to algorithms, allowing environmental groups to understand and validate calculations easily.
Lack of Audit Support:
Risk: Difficulty in tracking changes and maintaining an audit trail.
Solution: The 8864 Data Controller automatically logs system design changes, ensuring compliance with audit requirements and providing a comprehensive record of historical changes.
Lack of Timely Calibration:
Risk: Reactive decision-making due to delays in identifying calibration issues.
Solution: The 8864 Data Controller provides alarms based on validated data, enabling proactive identification and resolution of calibration issues.
Reactive Decision-Making:
Risk: Inefficiencies resulting from reactive problem-solving.
Solution: The 8864 facilitates proactive decision-making by constantly sharing validated and calculated values through various channels, including dashboards and reports.
In summary, the 8864 Data Controller offers a comprehensive solution for refineries to mitigate the risks associated with traditional data management systems in their operations and ultimately comply with the EPA’s 40 CFR Part 63 (MACT CC) requirements via the Refinery Sector Rule.
By leveraging its specialized functionality, automation capabilities, and robust audit support, refineries can streamline compliance efforts and avoid the challenges of utilizing Plant Process Systems for data acquisition. Additionally, StackVision, when paired with the 8864, further enhances visibility and control, making it an indispensable asset for modern refinery operations.
How ESC Spectrum Can Help Refineries
For more information on how the ESC Spectrum DAS (StackVision paired with the 8864 Data Controller) is useful to refineries, read our blog posts “How StackVision Helps Refineries With RSR Regulations” and “Improving Operational Efficiency with Data Acquisition Systems in Refineries”.
To learn more about the various solutions that we offer for refineries, visit our Refining Page. ESC Spectrum has staff with decades of professional experience providing systems that meet the unique requirements of the refining and petrochemical industries.
If you think your facility would benefit from implementing our DAS solutions, contact us today for more information.
For a complete resource on emissions monitoring, explore our Comprehensive Emissions Monitoring Guide for Refining and Petrochemical Facilities, covering everything from best practices to regulatory compliance.
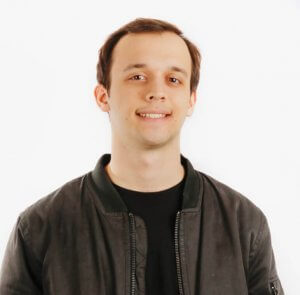
Dan Napolitan - Marketing Specialist I
Daniel joined ESC Spectrum in August of 2023 as a Marketing Specialist I. He started this position shortly after graduating from the University of Missouri with a degree in Journalism and Strategic Communications. Prior to working with ESC Spectrum, Daniel gained experience in the digital marketing field doing SEO and keyword research to produce successful organic content. He is now responsible for completing various marketing tasks such as blog writing, social media posts, paid search advertisements, web analytics, and more.